Un equipo multidisciplinario de la prestigiosa casa de estudios fabricó un elemento que entrega datos en tiempo real sobre variables como su temperatura, humedad y resistencia, los que servirán para determinar aspectos como su vida útil y así, comprender de mejor forma el comportamiento en terreno de este tipo de infraestructura.
En los últimos años, el desarrollo de la construcción con hormigón impreso 3D ha visto notables avances, ya sea en términos de equipos (impresoras cada vez más grandes, capaces de “imprimir” elementos masivos), diseño del material (el uso, por ejemplo, de áridos reciclados para el hormigón a utilizar) e incluso, el desarrollo de nuevas metodologías que optimicen la fabricación de elementos bajo esta metodología, entre otros desarrollos.
Sin embargo, el gran desafío que tiene esta tecnología es su aplicación a nivel industrial. Si bien existen ejemplos, estos son limitados y la gran mayoría de estas investigaciones y desarrollos aún no se incorporan de manera decidida dentro la planificación de un proyecto.
Esto podría cambiar gracias al trabajo desarrollado por un equipo del Departamento de Ingeniería de la prestigiosa Universidad de Cambridge liderado por el académico Abir Al-Tabaa, que en los últimos seis años desarrollaron una interesante tecnología que permite al elemento de hormigón impreso 3D “comunicar” en tiempo real datos como su temperatura, esfuerzo y presión gracias a sensores embebidos en su estructura.
Para probar esta tecnología, se “imprimió” un muro de cabecera -que, en el fondo, es un muro de contención que se instalan en la entrada o salida de tuberías de drenaje o alcantarillados y que, una vez instalados, reducen la erosión de la tubería y del área circundante provocada por el fujo de agua- en la autopista A30 en Cornwall, Inglaterra, convirtiéndose en el primer elemento de hormigón impreso 3D en ese país que se utiliza para infraestructura civil.
Hormigón impreso 3D para optimizar la infraestructura vial
El cambio de tecnología no es menor ya que, en su mayoría, este tipo de muros -que poseen una forma más bien limitada- son prefabricados de hormigón que cuentan con un alto contenido de acero de refuerzo. Al utilizar la impresión 3D, el equipo de la Universidad de Cambridge pudo diseñar y construir este elemento curvo y hueco, sin utilizar encofrados y también, sin acero para el refuerzo. La resistencia del muro proviene de la geometría del muro y no del acero, explicó el equipo en el comunicado de prensa.
Asimismo, detallaron que el muro, que se “imprimió” en el lapso de una hora, posee una altura de dos metros y un ancho de 3,5 metros. El elemento se fabricó en Gloucestershire, en las oficinas de la empresa Versarien, utilizando una impresora de brazo robótico.
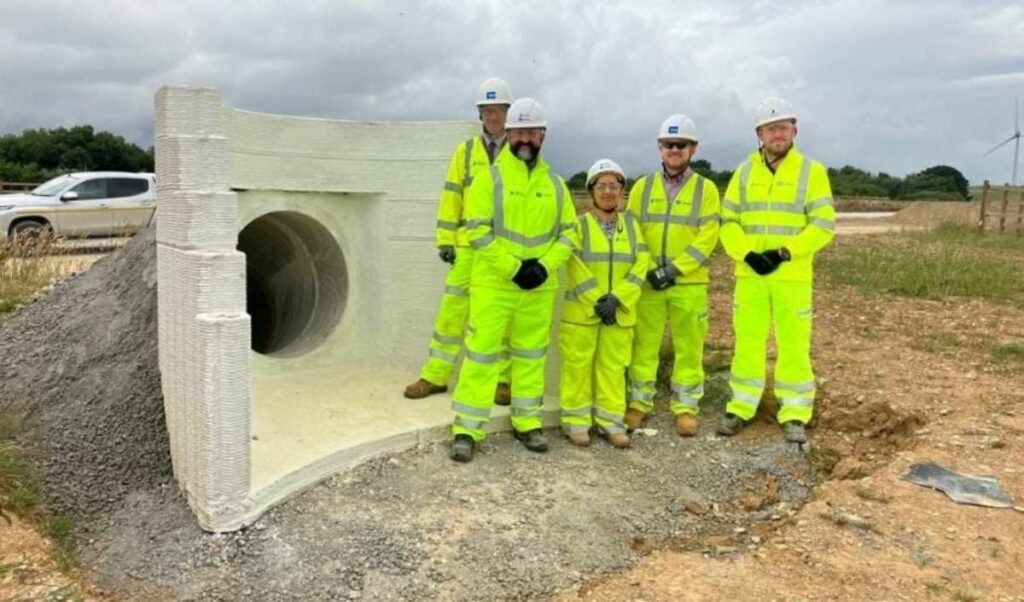
Además de utilizar la primera estructura de hormigón impreso 3D para infraestructura civil, el equipo también desarrolló un sistema de monitoreo que fuese entregando datos en tiempo real sobre aspectos tan relevantes como la temperatura, la que puede variar en las distintas capas del muro impreso.
“Para la impresión de hormigón 3D, se necesita un material que se asiente de manera muy rápida, lo que también genera una enorme cantidad de calor”, precisó el profesor Abir Al-Tabaa. “Por ello, embebimos nuestros sensores en el muro para medir la temperatura durante el proceso constructivo y ahora, obtenemos datos de ellos mientras el muro ya está en el sitio de la obra”.
Sensores especiales que permiten “hablar” al hormigón impreso 3D
Pese a su importancia, la temperatura no es el único dato que miden los sensores embebidos en el muro de cabecera. También, entregan información sobre humedad relativa, presión, esfuerzo, resistencia eléctrica y potencial termoeléctrico. De acuerdo con el equipo de investigadores, estos datos brindarán importante información respecto a la fiabilidad, robustez, precisión y durabilidad de los sensores, equipos que fueron desarrollados para monitorear la respuesta a la impedancia electromecánica y cuya función es monitorear las variaciones en estas mediciones a través del tiempo para detectar posibles daños.
Así, los sensores -bautizados como PZT por su materialidad- pueden mostrar cómo se endurece el hormigón impreso 3D en el tiempo y de forma simultánea, monitorear la “salud” de la estructura que los alberga, en este caso, el muro de cabecera.
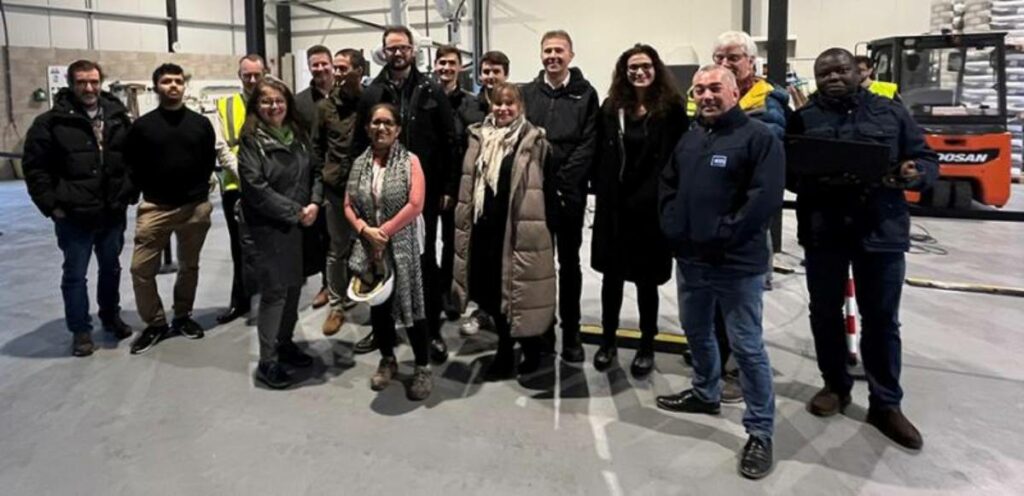
Además, durante el proceso de impresión del muro, se utilizó el sistema de tipografía digital conocido como LiDAR para escanear al elemento para así, crear un modelo 3D en la nube. “Hacer que el muro sea digital significa que nos puede hablar”, comentó Al-Tabaa. “Y podemos utilizar nuestros sensores para comprender de mejor forma a estas estructuras 3D e impulsar su aceptación en la industria”.
En ese sentido, el académico subrayó que “este proyecto servirá como un laboratorio viviente, generando información de alto valor sobre la vida útil del muro. Tanto los sensores como el modelo digital ayudarán a los profesionales en infraestructura a comprender de mejor forma como la impresión 3D puede usarse y adaptarse para imprimir elementos en base a cemento más grandes y complejos para la red estratégica de carreteras”.