Desde hace algunos años, el sector cementero en el Viejo Continente comenzó a incorporar el proceso del coprocesamiento para la reducción de CO2 en la producción del clínker, materia prima fundamental para la fabricación del cemento. En este artículo, se analiza -a través de los datos e información de CEMBUREAU- el impacto que está teniendo el coprocesamiento en el desarrollo de la industria, su aporte a la sostenibilidad del sector y los pasos a seguir para incrementar su participación.
La industria cementera europea, al igual que en otras regiones del mundo (incluyendo Chile), busca reducir su impacto en el medio ambiente y contribuir de manera decidida a mitigar los efectos del cambio climático.
En ese sentido, el sector lleva ya varias décadas utilizando un proceso conocido como “coprocesamiento”, el que, por una parte, cambia la manera en que se disponen los residuos, evitando que estos terminen en vertederos y, al mismo tiempo, permite la reutilización (o más bien, reciclaje) de estos en nuevos procesos para la producción de cemento y hormigón, mientras contribuye a la sostenibilidad ambiental.
De esta manera, el coprocesamiento, que combina el reciclaje de materiales con la recuperación energética, representa una de las estrategias fundamentales que tiene el sector cementero, tanto europeo como el local, para avanzar hacia la descarbonización de uno de los sectores industriales más intensivos en emisiones de CO2.
Qué es el coprocesamiento
Como se menciona antes, el coprocesamiento es la combinación simultánea de reciclaje de materiales y recuperación energética de residuos en un proceso térmico. Este proceso permite sustituir recursos minerales naturales y combustibles fósiles como el carbón y los derivados del petróleo por materiales alternativos derivados de residuos.
De acuerdo con CEMBUREAU, la Asociación Europea del Cemento, la implementación de esta práctica en el sector genera impactos positivos y, lo que para el gremio es aún mejor, significativos en la sostenibilidad de la industria cementera en Europa. Esto, porque el coprocesamiento permite reducir la dependencia a combustibles fósiles vírgenes, disminuir la intensidad de CO2 en la fabricación de cemento, reducir la cantidad de residuos que van a vertederos y minimizar los costos de inversión pública en nuevas instalaciones dedicadas.
El proceso de coprocesamiento aprovecha las características que poseen los hornos cementeros, que operan a temperaturas extremadamente altas (hasta 1.450°C) para producir el clínker -materia prima esencial en la fabricación del cemento- y tienen tiempos de residencia prolongados.
Estas condiciones, dicen desde CEMBUREAU, garantizan la destrucción completa de los componentes orgánicos de los residuos, mientras que los componentes minerales se incorporan a la matriz del clínker, convirtiéndose en parte integral del producto final.
Una transformación real
Los datos que entrega la multigremial cementera de Europa revelan el aporte que el coprocesamiento realiza para las ambiciosas metas, en materia de sostenibilidad, que se planteó la industria en el Viejo Continente. En la actualidad, el sector cementero europeo sustituye en promedio un promedio del 53% de su combustible con fuentes alternativas, y aspira a incrementar aún más este porcentaje. Estudios técnicos corroborados por el gremio demuestran que no existen barreras técnicas para elevar esta tasa al 60% en toda Europa para 2030.
La evolución, en ese sentido, es decidora: en 1990, apenas el 2% de la energía térmica en el sector cementero de la Unión Europea (UE) provenía de combustibles alternativos. Para el año 2000, este porcentaje aumentó al 9%, y continuó creciendo de manera constante: 28% en 2009, 39% en 2012, 46% en 2016, y finalmente 53% en 2021. Esto representa un incremento de 1,1 millones de toneladas de combustibles alternativos en 1990 a 12,9 millones de toneladas en 2021.
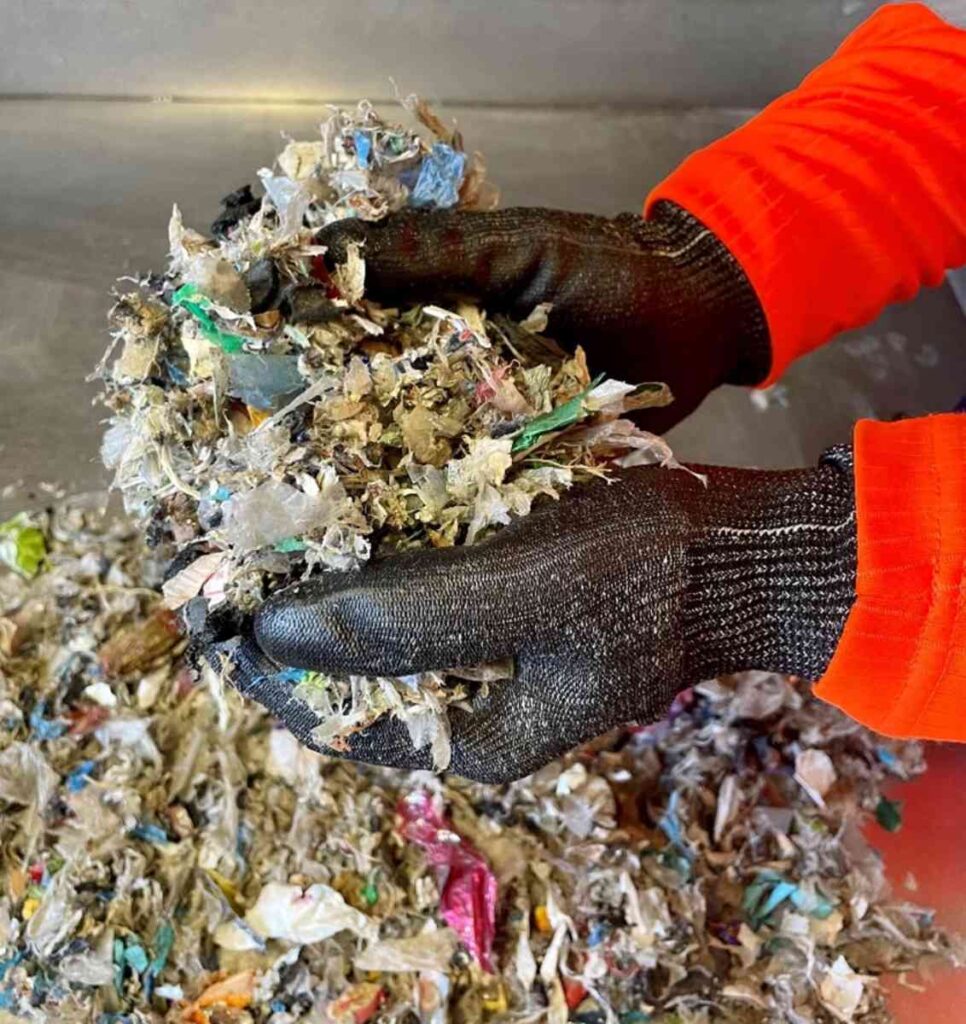
En términos de distribución geográfica, los avances, si bien prometedores, son un tanto dispares. Según los datos que presentó la agrupación gremial en 2021, varios países europeos destacan por sus altas tasas de sustitución térmica con combustibles alternativos: Austria, Alemania y Polonia lideran con un 76% cada uno, seguidos por la República Checa con un 70%. La media de la UE se sitúa en el 53%, mientras que otros países como Suecia (46%), Francia (46%), Italia (39%) y España (19%) muestran diferentes niveles de adopción.
En ese sentido, varias plantas cementeras en Europa han alcanzado tasas de sustitución del 100%, como es el caso de instalaciones en Austria, República Checa y Reino Unido. Otras plantas en Polonia y Alemania han logrado tasas superiores al 90%.
Coprocesamiento: beneficios ambientales cuantificables
El impacto ambiental positivo del coprocesamiento es considerable. Los estudios de la asociación gremial reportan que esta práctica evita 23 millones de toneladas de emisiones de CO2 cada año. Esta reducción se logra principalmente a través de dos mecanismos: la sustitución de combustibles fósiles por alternativas con menor factor de emisión de carbono y el uso de biomasa, que se considera carbono neutral.
Además, el uso de combustibles alternativos permite ahorrar aproximadamente 7,8 millones de toneladas de carbón anualmente. Esta cifra es particularmente significativa considerando que el carbón es uno de los combustibles fósiles con mayor intensidad de carbono.
Un aspecto menos conocido, pero igualmente importante, es que aproximadamente el 5% de las materias primas necesarias para la producción del clínker de cemento en Europa consiste en material reciclado y cenizas procedentes de combustibles alternativos. Esto representa una contribución significativa a la economía circular europea, reduciendo la necesidad de extraer materias primas para su producción, como caliza, arcilla, arena y mineral de hierro.
El coprocesamiento también contribuye significativamente a la gestión de residuos en Europa. Al desviar residuos de los vertederos, se reducen las emisiones de metano asociadas con la descomposición de materiales orgánicos en condiciones anaeróbicas. El metano es un gas de efecto invernadero con un potencial de calentamiento global aproximadamente 25 veces mayor que el CO2 en un horizonte de 100 años, por lo que evitar estas emisiones representa un beneficio climático sustancial.
¿Cómo funcional el coprocesamiento en la industria cementera?
El coprocesamiento en la industria cementera implica una serie de pasos técnicos cuidadosamente controlados. En primer lugar, los residuos deben ser caracterizados y pretratados para garantizar que cumplan con especificaciones estrictas en términos de poder calorífico, contenido de humedad, tamaño de partícula y composición química.
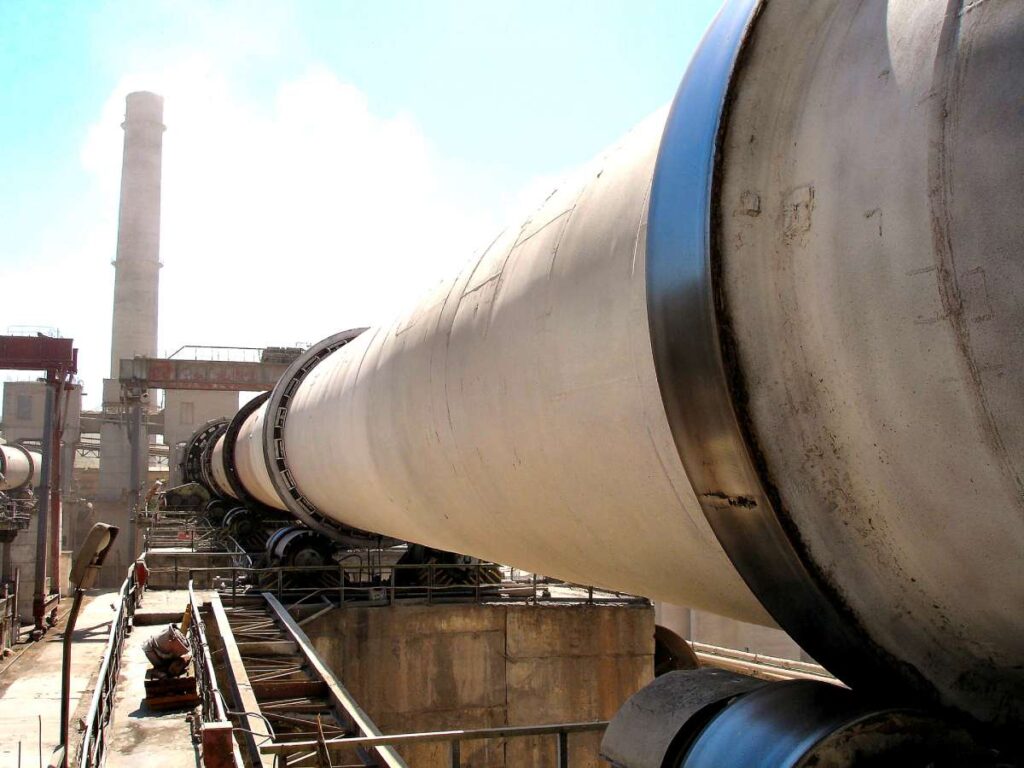
En los hornos cementeros de toda Europa se coprocesa una amplia variedad de residuos: neumáticos usados, madera, plásticos no reciclables, productos químicos y otros tipos de desechos. Estos materiales son co-combustionados en los hornos, donde se aprovecha su valor calorífico para sustituir combustibles fósiles.
El proceso de fabricación de cemento es particularmente adecuado para el coprocesamiento debido a varias características técnicas:
- Altas temperaturas: Los hornos de cemento operan a temperaturas extremadamente altas (hasta 1.450°C), lo que garantiza la destrucción completa de compuestos orgánicos, incluidos contaminantes persistentes.
- Ambiente alcalino: El ambiente alcalino dentro del horno neutraliza compuestos ácidos, reduciendo las emisiones de gases ácidos como SOx y HCl.
- Tiempo de residencia prolongado: Los gases permanecen a altas temperaturas (>850°C) durante varios segundos, asegurando una combustión completa y minimizando las emisiones de compuestos orgánicos volátiles.
- Efecto de retención de cenizas: A diferencia de los incineradores convencionales, donde las cenizas se convierten en un residuo que requiere gestión adicional, en los hornos cementeros las cenizas se incorporan completamente a la matriz del clínker, convirtiéndose en parte integral del producto final.
Lo que hace único al coprocesamiento es que, a diferencia de la incineración convencional, no genera residuos adicionales que requieran tratamiento o eliminación. Dentro de un horno, los combustibles residuales son coprocesados, utilizando el valor calorífico derivado del combustible residual para sustituir combustibles fósiles e incorporando las cenizas como sustituto parcial de materias primas, sin dejar residuos.
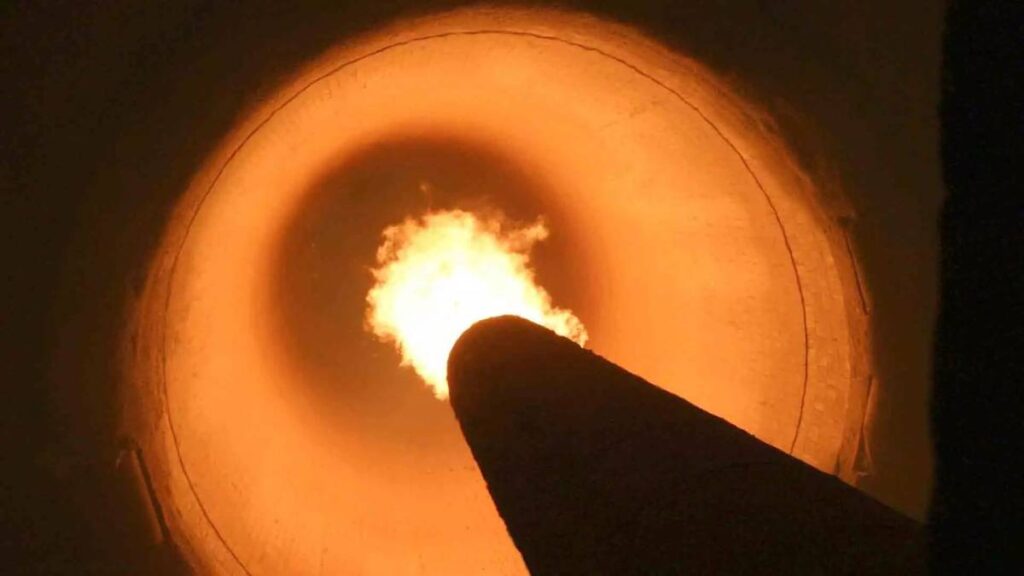
Esta característica posiciona al coprocesamiento como una solución de gestión de residuos más eficiente que el vertido o la incineración, convirtiendo a la industria cementera en un consumidor neto de residuos y, por lo tanto, en un actor clave en la economía circular.
Tipos de residuos utilizados en el coprocesamiento
La variedad de residuos que pueden ser utilizados en el coprocesamiento es amplia, aunque sujeta a estrictos controles de calidad y limitaciones técnicas. Entre los principales tipos de residuos utilizados se encuentran:
- Neumáticos fuera de uso: Los neumáticos tienen un alto poder calorífico (comparable al del carbón) y un contenido significativo de hierro que se incorpora al clínker. Europa genera aproximadamente 3 millones de toneladas de neumáticos usados anualmente, una parte significativa de los cuales se destina al coprocesamiento.
- Residuos de madera: Incluyen madera tratada, pintada o contaminada que no es adecuada para el reciclaje convencional. La madera es particularmente valiosa como combustible alternativo debido a su alto contenido de biomasa.
- Plásticos no reciclables: Fracciones de residuos plásticos que no pueden ser reciclados mecánicamente debido a su composición, contaminación o complejidad. Estos plásticos tienen un alto poder calorífico y pueden sustituir eficazmente a los combustibles fósiles.
- Lodos de depuradora: Los lodos deshidratados o secos de plantas de tratamiento de aguas residuales pueden ser utilizados como combustible alternativo, aprovechando su contenido energético mientras se gestionan de manera ambientalmente responsable.
- Residuos agrícolas y forestales: Incluyen cáscaras, huesos de frutas, residuos de poda y otros materiales biomásicos que aportan energía renovable al proceso.
- Combustibles derivados de residuos (CDR/SRF): Preparados a partir de fracciones no reciclables de residuos municipales e industriales, estos combustibles procesados tienen propiedades estandarizadas que facilitan su uso en hornos de cemento.
- Residuos peligrosos: Ciertos residuos peligrosos, como solventes usados, aceites usados y residuos de la industria química, pueden ser gestionados de manera segura en hornos de cemento debido a las altas temperaturas y condiciones de combustión controladas.
La selección y mezcla adecuada de estos residuos es crucial para mantener la estabilidad del proceso de producción y la calidad del cemento, así como para cumplir con los límites de emisiones establecidos en la normativa europea.
Casos de éxito en Europa
CEMBUREAU documenta varios casos de éxito en toda Europa que ilustran el potencial y la diversidad de aplicaciones del coprocesamiento. Estos son algunos ejemplos:
Austria: Integración completa en la economía circular
En Austria, la planta de cemento Retznei alcanzó una tasa de coprocesamiento del 100% y un 30% de reciclaje de materias primas. Esta instalación, ubicada en Estiria meridional, estableció una asociación con ThermoTeam, que produce 100.000 toneladas de combustible derivado de residuos (RDF) anualmente. Las colaboraciones con sectores como la pulpa y papel y la industria farmacéutica han sido fundamentales para mantener los flujos de residuos circulares.
Además, el 38% de la mezcla de combustibles de la planta es biogénica y hasta el 30% de sus materias primas provienen de productos reciclados. La planta también ha implementado un sistema de recuperación de calor que reutiliza el exceso de calor de la producción de clínker para calentar hogares y edificios locales, mientras que las instalaciones solares satisfacen el 10% del consumo máximo de energía.
Reino Unido: Eliminación completa de combustibles fósiles
En el Reino Unido, CEMEX inauguró su instalación de Climafuel en la planta de cemento de Rugby, permitiendo que ésta opere con 100% de combustibles alternativos. Climafuel es un combustible derivado de residuos creado a partir de residuos domésticos y comerciales que de otro modo terminarían en vertederos.
Esta inversión representa un hito significativo en la estrategia global de descarbonización de CEMEX, demostrando que es técnicamente posible eliminar por completo el uso de combustibles fósiles en la producción de cemento.
Grecia: Tecnología avanzada para la reducción de emisiones
En Grecia, la planta de cemento Kamari del Grupo TITAN completó recientemente una inversión verde de 26 millones de euros con la instalación de tecnología de precalcinación avanzada. Esta nueva tecnología reducirá las emisiones anuales de CO2 en 150.000 toneladas y permitirá un mayor uso de combustibles alternativos, alcanzando tasas de sustitución térmica superiores al 70% para uno de sus hornos rotatorios y por encima del 55% para toda la planta.
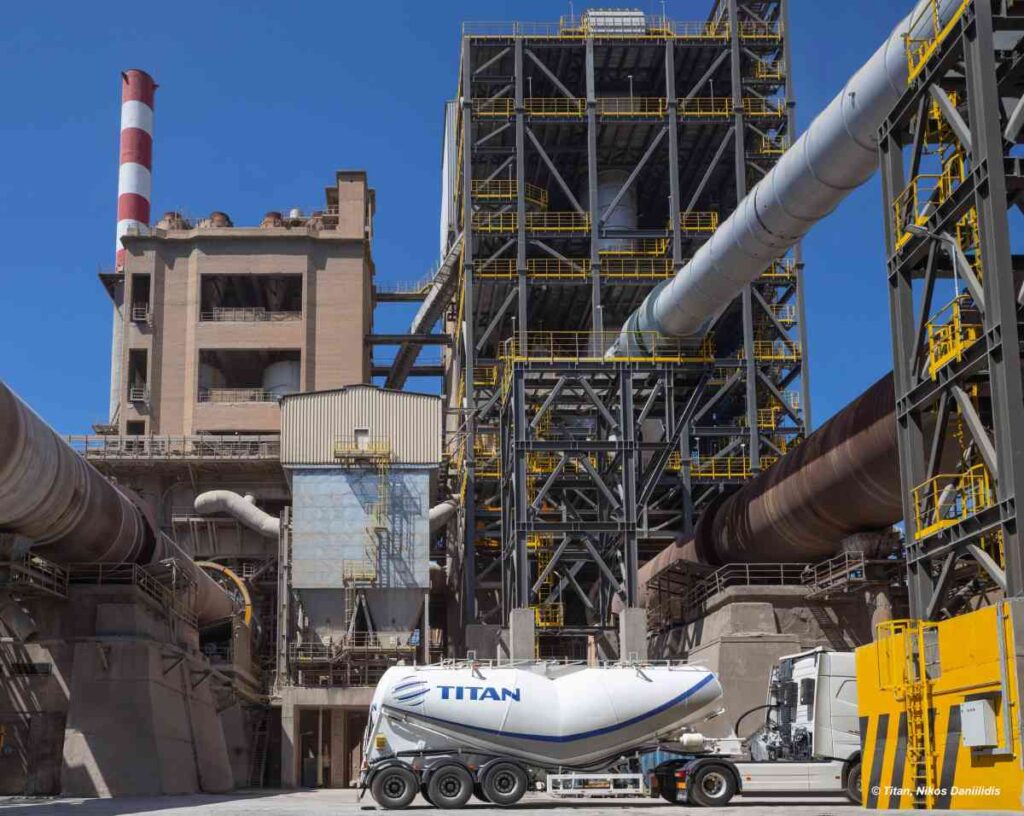
El impacto de esta inversión se extiende más allá de los muros de la planta, llegando a la región circundante de Ática. Al integrar residuos sólidos urbanos reciclados como combustibles alternativos, la planta juega un papel crucial en la gestión integral de residuos, fomentando el reciclaje y defendiendo los principios de la economía circular.
Hungría: Innovación tecnológica para optimizar el uso de combustibles alternativos
En Hungría, Holcim invirtió 11 millones de euros en esfuerzos de protección ambiental, logrando una sustitución del 90% de combustibles fósiles por fuentes alternativas. Entre las inversiones clave se incluyen el desarrollo de un almacén de combustibles alternativos y una línea de alimentación cerrada, así como la implementación de tecnología innovadora de secado rápido para optimizar la eficiencia del combustible.
Esta tecnología se utiliza para mejorar el valor calorífico del combustible alternativo finamente triturado, conocido como Combustible Derivado de Residuos (RDF). Al mejorar el valor calorífico, se puede extraer más energía de los residuos, reduciendo así la necesidad de combustibles fósiles tradicionales y apoyando la reducción de emisiones de carbono.
Letonia: Remediación ambiental a través del coprocesamiento
En Letonia, SCHWENK Latvija participó en una importante iniciativa ambiental entre 2018 y 2022: la limpieza de las balsas de alquitrán de Inčukalns, un área históricamente contaminada. Aproximadamente 50.000 toneladas de suelo contaminado neutralizado se utilizaron como combustible alternativo en la planta de cemento de Broceni durante el proyecto.
El proceso de limpieza implicó extraer alquitrán ácido de las balsas y neutralizarlo in situ para que fuera seguro como parte de una mezcla de combustible alternativo. Después de la neutralización, el suelo fue transportado a la planta de Broceni y almacenado de forma segura. El proyecto, que se completó en 2022, demuestra la transformación exitosa de un desafío ambiental en una solución innovadora para fuentes de combustible alternativas.
Coprocesamiento y economía circular
Debido a sus características y a lo que abarca este proceso, el coprocesamiento representa un ejemplo claro de economía circular dentro de la industria cementera. Además, el hecho que la industria del Viejo Continente lo tenga dentro de sus estrategias para la descarbonzación del sector, va en línea con los principios de jerarquía de gestión de residuos de la UE y las ambiciones del Pacto Verde Europeo.
Reciclaje de materiales en Irlanda
En Irlanda, la planta de Irish Cement en Platin utiliza Combustible Sólido Recuperado (SRF) creado a partir de residuos no reciclables como papel, plástico y envases compuestos. En 2022, el 57% de la energía térmica necesaria para la producción de cemento provino de este tipo de combustible.
Un aspecto particularmente innovador es el aprovechamiento de la fracción no combustible del SRF como materia prima en el horno. El contenido de aluminio en el SRF, que proviene típicamente de envases con revestimiento de aluminio, se incorpora al clínker de cemento, reduciendo la necesidad de bauxita extraída y transportada. Desde 2011, este proceso disminuyó las importaciones de bauxita en aproximadamente 140.000 toneladas.
Este ejemplo de economía circular real destaca cómo los “residuos” se pueden transformar en recursos valiosos para, en este caso, la producción de cemento, bajando así la demanda de materias primas. La práctica de la planta de Platin de obtener aluminio proveniente del SRF realiza una contribución importante a la producción sostenible de cemento de alta calidad.
Restauración de la biodiversidad en Bélgica
En Bélgica, un proyecto conjunto entre las empresas Electrabel, Cementir Holding y Heidelberg Materials inició el reciclaje de cenizas volantes provenientes de un antiguo depósito debido a su alto contenido de alúmina (Al2O3). El objetivo de este proyecto es eliminar un depósito de 2,3 millones de toneladas del material entre 2017 y 2029, con el fin último de restaurar el sitio a su biodiversidad natural original.
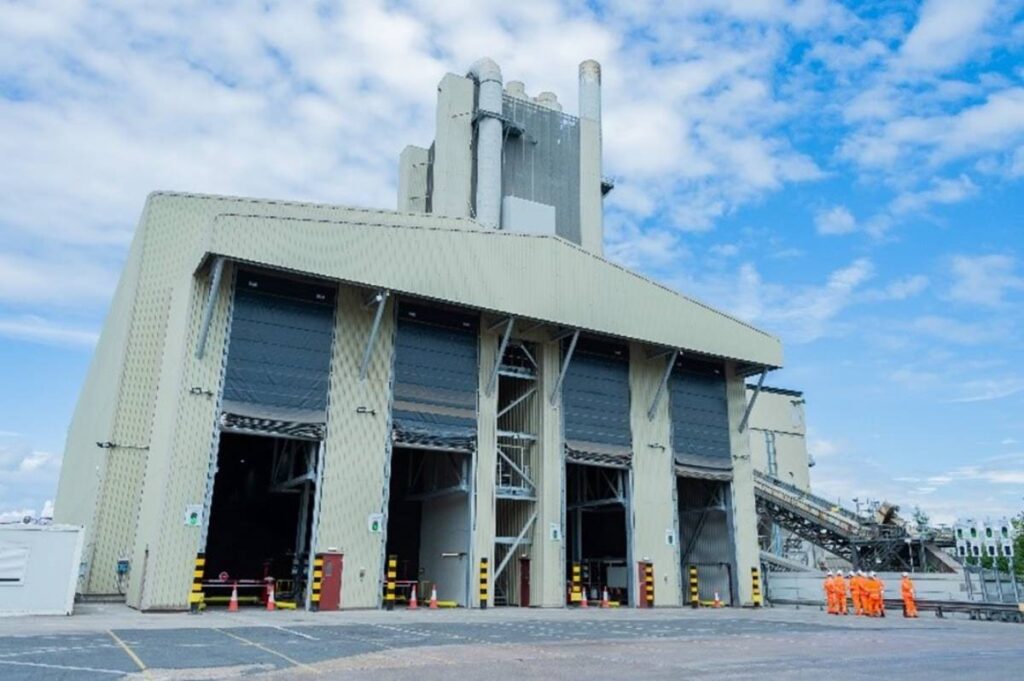
Los datos evidencian que, a la fecha, el proyecto superó con éxito las limitaciones ambientales y locales, lo que resultó en la construcción de instalaciones temporales, como una cinta transportadora cerrada de 1,7 km de longitud que facilita la eliminación de las cenizas a través de vías fluviales.
Integración en la gestión de residuos urbanos en Italia
En Italia, la planta de cemento de Buzzi Unicem en la localidad de Robilante utiliza Combustible Sólido Recuperado (SRF) que comprende entre un 40% a un 50% de biomasa -que es carbono neutral- lo que se traduce en una reducción tanto las emisiones directas como indirectas de CO2.
Bajo en nitrógeno y azufre, el SRF aporta a la reducción de las emisiones de NOx y SO2, mientras ofrece una solución más rentable para la producción de clínker que los combustibles fósiles tradicionales.
En ese sentido, la planta cementera Robilante forma parte integral del plan local de gestión de residuos, utilizando residuos urbanos no clasificados convertidos en SRF, complementando así los procesos de reciclaje que tiene implementados el gobierno local de Robilante.
Aspectos técnicos del control de emisiones
Un aspecto fundamental en el proceso del coprocesamiento se encuentra en el estricto control de emisiones para garantizar que no haya impactos negativos en la calidad del aire. En ese sentido, las plantas cementeras que utilizan combustibles alternativos están sujetas a la Directiva de Emisiones Industriales de la UE y deben cumplir con límites de emisión estrictos.
Las tecnologías de control de emisiones empleadas en las plantas modernas incluyen:
- Precipitadores electrostáticos y filtros de mangas: Estas tecnologías capturan partículas finas con eficiencias superiores al 99,9%, asegurando que las emisiones de polvo se mantengan muy por debajo de los límites legales.
- Sistemas de reducción catalítica selectiva (SCR) y reducción no catalítica selectiva (SNCR): Permiten la reducción de emisiones de óxidos de nitrógeno (NOx) mediante la inyección de amoníaco o urea en los gases de combustión.
- Absorbedores de cal: Utilizados para neutralizar gases ácidos como el dióxido de azufre (SO₂) y el ácido clorhídrico (HCl).
- Inyección de carbón activado: Esta técnica se emplea para capturar metales pesados volátiles y compuestos orgánicos persistentes como dioxinas y furanos.
- Sistemas de monitoreo continuo de emisiones (CEMS): Estos sistemas proporcionan datos en tiempo real sobre las emisiones, permitiendo ajustes inmediatos en el proceso si es necesario.
Gracias a estas tecnologías avanzadas, las plantas cementeras modernas pueden utilizar combustibles alternativos sin comprometer la calidad del aire local. De hecho, en muchos casos, la modernización de las plantas para permitir el coprocesamiento viene aparejada de mejoras significativas en las instalaciones, lo que incide en el rendimiento ambiental general.
Desafíos y perspectivas futuras
Si bien los avances que evidencia Europa en esta materia son prometedores, el sector enfrenta desafíos significativos para expandir aún más el coprocesamiento. Estos incluyen:
- Barreras regulatorias y administrativas
En algunos países europeos, los procedimientos de autorización para el coprocesamiento son complejos y prolongados, lo que puede desalentar las inversiones. La armonización de los marcos regulatorios en toda la UE podría acelerar la adopción de esta práctica.
- Percepción pública
La percepción pública sigue siendo un obstáculo en algunos países. Existe una confusión frecuente entre lo que es el coprocesamiento y la incineración convencional, lo que puede generar oposición local a proyectos que involucran el uso de residuos en plantas de cemento. La educación y la transparencia son fundamentales para abordar estas preocupaciones.
- Disponibilidad y calidad de los residuos
La disponibilidad y calidad de los residuos adecuados para el coprocesamiento varía considerablemente entre regiones. Además, la competencia por ciertos flujos de residuos está aumentando a medida que más industrias buscan alternativas sostenibles.
- Inversiones necesarias
La adaptación de las plantas existentes para incrementar el uso de combustibles alternativos requiere inversiones significativas en infraestructura de almacenamiento, sistemas de alimentación y tecnologías de control de emisiones. El retorno de estas inversiones depende en gran medida de los precios relativos de los combustibles fósiles y alternativos, así como de marcos regulatorios que incentiven y apoyen este tipo de proyectos.
No obstante, las perspectivas son prometedoras. El potencial del coprocesamiento puede mejorarse aún más con medidas regulatorias eficientes que reconozcan esta forma de reciclaje de materiales y su contribución a los objetivos de reciclaje de Europa, como apunta CEMBUREAU.
La evolución del uso de combustibles alternativos en el sector cementero de la UE muestra una tendencia claramente ascendente, pasando de 1,1 millones de toneladas en 1990 a 12,9 millones de toneladas en 2021. Esta progresión constante sugiere que existe margen para un mayor crecimiento en los próximos años.
- Innovación tecnológica continua
La adopción del coprocesamiento ha impulsado importantes innovaciones tecnológicas en el sector. Las plantas cementeras están implementando tecnologías avanzadas para optimizar el uso de combustibles alternativos y reducir aún más su huella ambiental.
Optimización de procesos en Polonia
Un ejemplo que ilustra la influencia positiva del coprocesamiento, acompañado de políticas públicas eficientes, se puede encontrar en la planta de cemento de Cemex en la localidad de Rudniki, Polonia, donde se puede ver el éxito de los recientes esfuerzos de modernización destinados a aumentar la sustitución de combustibles fósiles con combustibles alternativos del 55% al 75%. Este objetivo, informan desde CEMBUREAU, se logró superar con combustibles alternativos que ahora representan más del 90% de los combustibles del proceso de producción, lo que le valió a la planta el segundo lugar a nivel mundial dentro del Grupo Cemex.
Además, los esfuerzos de modernización resultaron en una disminución del 21% en el consumo unitario de calor, una reducción del 17% en las emisiones de dióxido de carbono por tonelada y también, se tradujeron en ahorros significativos en costos. También, gracias al uso de aditivos alternativos, la planta disminuyó en un 63% la proporción de clínker en el cemento, utilizando materias primas residuales descarbonizadas que ahora representan más del 13% de la entrada de material del clínker.
Integración de materiales secundarios en España
Otro caso para tener en consideración se encuentra en la ciudad de Lemona, España. Cementos Lemona, una empresa de CRH con más de un siglo de experiencia en la producción de cemento, ejemplifica cómo estos procesos pueden adaptarse para mejorar la sostenibilidad. La empresa integró la Escoria de Horno de Cuchara (LFS), un subproducto de la fabricación de acero, en su proceso de fabricación como materia prima secundaria.
Este tipo de escoria, abundante en las fábricas de acero de arco eléctrico del norte de España, posee un alto contenido de cal. Este atributo permite a Cementos Lemona reducir la cantidad de piedra caliza para la producción de clínker, disminuyendo así las emisiones relacionadas. Además, la escoria LFS es rica en componentes esenciales para el clínker de cemento, como sílice (15%), alúmina (10%) y óxido de hierro (6%).
La utilización de esta escoria beneficia a Cementos Lemona de dos formas. Primero, sus propiedades descarbonatadas ayudan a la empresa a reducir sus emisiones de CO2. Segundo, el material contribuye a la economía circular de la región al evitar que la escoria LFS termine en vertederos. Por lo tanto, su uso ofrece un ejemplo claro de cómo las prácticas innovadoras pueden alinear la producción industrial con la sostenibilidad ambiental.
El papel del coprocesamiento en la descarbonización del sector cementero
El coprocesamiento juega un importante rol en las estrategias de descarbonización del sector cementero europeo. De acuerdo con la hoja de ruta de CEMBUREAU para alcanzar la carbono neutralidad al año 2050, el uso de combustibles alternativos podría contribuir aproximadamente al 16% de la reducción total de emisiones necesaria.
En el mismo documento, la asociación puntualiza que el coprocesamiento es sólo una parte de una estrategia más amplia que también incluye:
- Eficiencia energética: Mejoras en la eficiencia térmica y eléctrica de las plantas.
- Sustitución de clínker: Reducción del contenido de clínker en el cemento mediante el uso de materiales cementantes suplementarios como cenizas volantes, escoria de alto horno y puzolanas naturales.
- Captura y utilización o almacenamiento de carbono (CCUS): Tecnologías para capturar el CO₂ emitido durante la producción de cemento y utilizarlo en otros procesos industriales o almacenarlo permanentemente.
- Nuevas tecnologías de cemento: Desarrollo de cementos alternativos con menor huella de carbono.
En ese sentido, el coprocesamiento funciona como un complemento a estas otras estrategias y, de acuerdo con la experiencia recogida en los proyectos destacados por CEMBUREAU, puede alcanzar beneficios a corto y medio plazo mientras se desarrollan y despliegan tecnologías más disruptivas, en especial, aquellas vinculadas a la captura o almacenamiento de CO2.
Un modelo de revalorización energética para la industria sostenible
Las altas tasas de coprocesamiento en la industria cementera europea -en ciertos proyectos, alcanzando el 100% de revalorización energética de residuos- entrega importantes lecciones para otros sectores industriales en los que el uso de energía es intensivo. Dados los casos de éxito, se demuestra que es posible conciliar las demandas de producción industrial con objetivos ambientales concretos mediante la innovación y el compromiso con la economía circular.
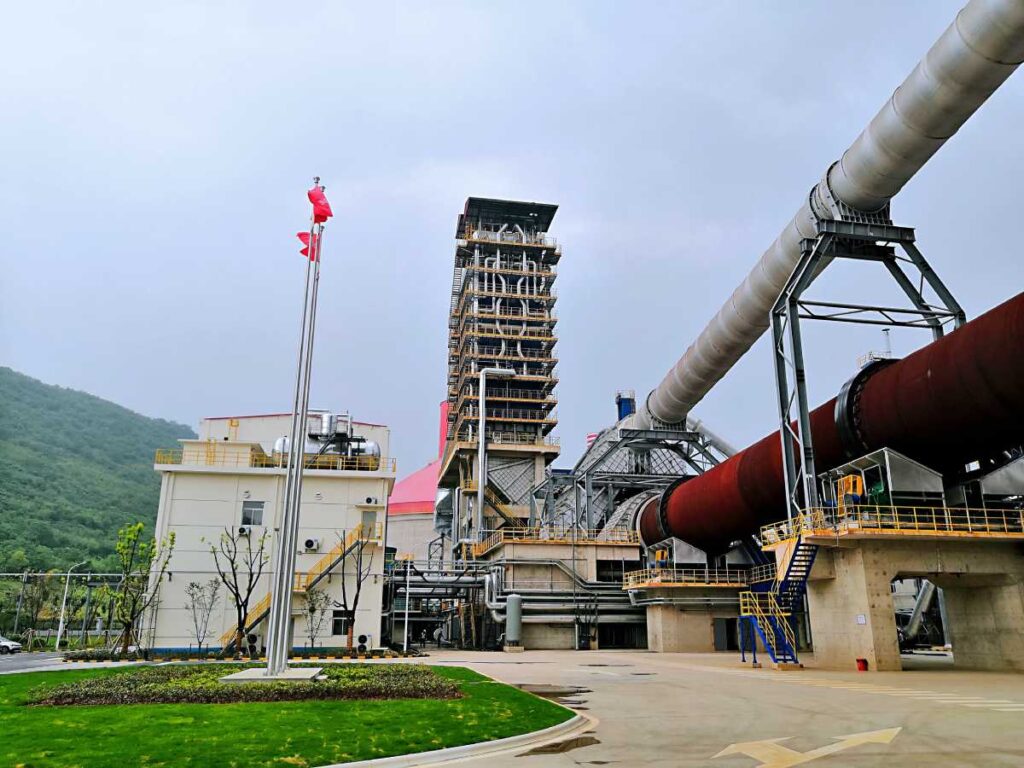
En ese sentido, los datos y ejemplos que entrega la Asociación Europea del Cemento, CEMBUREAU, evidencian que el sector ha logrado importantes avances en la sustitución de combustibles fósiles por alternativas más sostenibles, además de continuar trabajando para incrementar aún más las tasas de reemplazo. Esto refleja la posición de la industria cementera en el Viejo Continente en transformar la mentalidad del sector: de ver los residuos como un problema a considerarlos un recurso valioso.
El coprocesamiento representa una solución triple: reduce la dependencia de combustibles fósiles vírgenes, disminuye la intensidad de CO2 en la producción de cemento y reduce la cantidad de residuos que van a vertederos. En un momento en que Europa busca acelerar su transición hacia una economía circular y baja en carbono, el coprocesamiento emerge como un ejemplo concreto de cómo la industria cementera puede ser parte importante de la solución.